Table of Contents
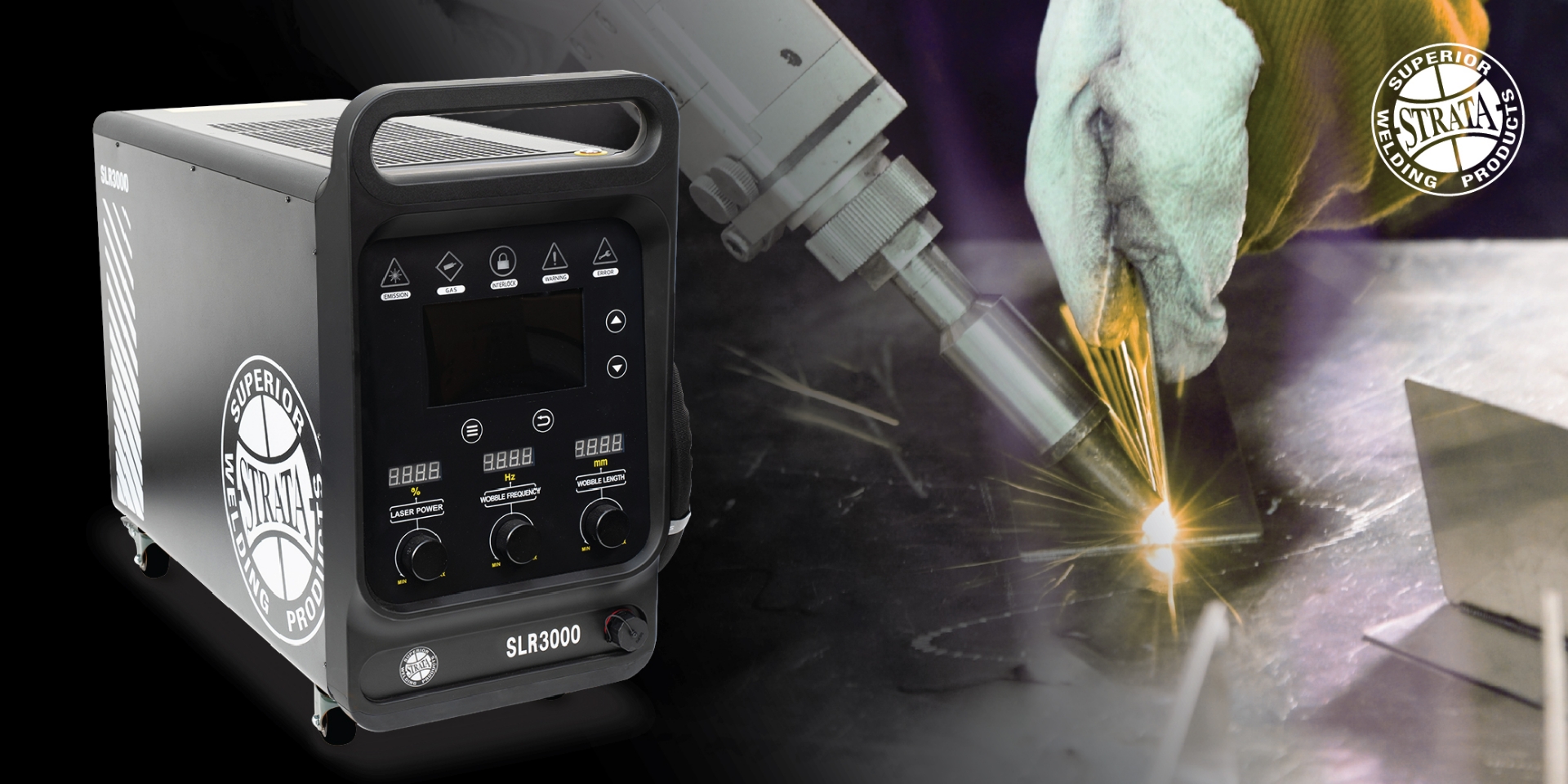
Laser welding has transformed metal fabrication, delivering precision, speed, and quality in various applications, from automotive and aerospace to electronics and medical devices. A key aspect of achieving high-quality welds is understanding and fine-tuning three critical parameters: laser power, material thickness, and welding speed. These elements form the foundation of a robust welding process that enhances weld integrity and boosts productivity in industrial workshops.
This guide dives into the essentials of laser welding, helping welding technicians and engineers make informed adjustments for optimal results. With the correct parameters and a deeper understanding of laser welding's nuances, welders can enhance precision and minimise defects, ensuring each project meets the highest standards.
Why Laser Welding is Ideal for Metal Fabrication
Laser welding is a high-precision joining method that uses a focused laser beam to fuse materials at targeted locations, producing deep, narrow welds with minimal thermal distortion. The laser's intensity reaches several thousand degrees Celsius, enough to melt metals instantly. When correctly applied, this process allows for controlled fusion with little impact on surrounding material, preserving its structural integrity.
Unlike traditional welding techniques, laser welding creates high-strength bonds without extensive heat-affected zones (HAZ). This characteristic makes it ideal for joining thin, heat-sensitive materials. The method is well-suited for high-volume applications, allowing industrial workshops to standardise quality across various projects. Additionally, the process works on multiple metals, although each type has specific requirements due to its thermal properties and absorption characteristics.
Laser Beam Focus and Material Interaction
The laser beam is the star player in laser welding. Its focus is adjusted based on the thickness and type of material, dictating the depth and profile of the weld. Different materials react uniquely to laser energy absorption, which affects weld quality. For example, stainless steel absorbs laser energy efficiently, allowing high-speed, precise welds. At the same time, highly reflective materials, like aluminium and copper, may require special lasers to overcome challenges associated with high reflectivity and thermal conductivity.
Key Laser Welding Parameters: Power, Thickness and Speed
Each laser welding job has unique requirements, and balancing parameters is critical. Misalignment in these settings can result in defects, weak welds, or damaged welded materials.
1. Laser Power
Laser power affects how deep the beam penetrates the material. Higher power is needed for thicker materials, while lower power settings suffice for thinner sections. Here’s a general guide to power requirements based on material thickness:
- Thin materials (<1.0mm): 500-1500 watts
- Moderate thickness (1.0-3.0mm): 1500-3000 watts
- Thick materials (>3.0mm): 3000-6000 watts
Fine-tuning power settings helps avoid burn-through on thin materials and ensures adequate penetration on thicker sections.
2. Welding Speed
Speed is a balancing act: too fast, and the weld may lack depth; too slow, and the heat could cause distortion. Welding speed generally ranges from 1 to 10 m/min, depending on the thickness and material.
- Thin materials (<1.0mm): Higher speeds (5-10 m/min) to prevent overheating
- Thicker materials (>3.0mm): Lower speeds (1-5 m/min) for more profound fusion
Finding the right speed for each job maintains weld consistency and minimises heat-affected zones.
Material | 1000 Watts | 1500 Watts | 2000 Watts |
Stainless Steel | 0.5mm-3mm | 0.5mm-4mm | 0.5mm-5mm |
Aluminium | 0.5mm-2mm | 0.5mm-3mm | 0.5mm-4mm |
Brass | 0.5mm-3mm | 0.5mm-6mm | 0.5mm-8mm |
Carbon Steel | 0.5mm-3mm | 0.5mm-4mm | 0.5mm-5mm |
This chart serves as a quick reference for welding professionals, helping them choose the correct parameters based on the material and thickness they’re working with. For instance, a 2mm stainless steel workpiece may require 1000 watts of power and a welding speed of around 600mm/s to achieve optimal results.
3. Focus Position
The laser's focus position determines how the beam's energy is distributed. For thin materials, focusing near the surface creates wider, shallower welds, while concentrating more bottomless suits thicker materials, resulting in narrow, deep penetration welds.
Adjusting ±1 mm in the focal position can significantly alter the weld profile, affecting its mechanical properties and appearance. Testing different focal positions on sample pieces helps refine the best setup.
Additionally, shielding gases like argon or helium is crucial to protecting the weld pool from contamination and ensuring a clean, strong joint. The choice of gas and its flow rate must be tailored to the material, with different gases offering varying benefits, such as deeper penetration or smoother weld surfaces.
Material Specific Guidelines
Each metal responds differently to laser welding, requiring tailored approaches to power, speed, and other parameters. Here are some tips for common metals:
1. Stainless Steel
Stainless steel is laser-friendly thanks to its high laser energy absorption rate, making it ideal for precision, high-speed applications. This metal typically requires moderate power settings with speeds up to 10 m/min for thin sections. A steady argon shielding gas flow (10-20 L/min) protects the weld pool, ensuring a smooth, consistent finish.
2. Aluminium
Aluminium's high reflectivity and thermal conductivity can make it challenging to weld. High-power fibre lasers are best suited for aluminium, providing the energy to penetrate effectively. Lower speeds (1-5 m/min) help manage heat distribution while using helium as a shielding gas (20-30 L/min) can improve weld depth and reduce reflectivity issues.
3. Brass and Copper
These materials are also highly reflective, necessitating techniques similar to those of aluminium. High-power fibre or green lasers (515 nm wavelength) are adequate, as they improve energy coupling. Copper, in particular, may require surface treatments like abrasion to enhance laser absorption.
Choosing the Right Laser Welder for the Job
Among the latest advancements in laser welding, the Strata Pro Series Laser Welders stand out for their compact, user-friendly design and powerful performance. The Strata SLR5000 model features a sophisticated "small core diameter" laser and a dual-circuit refrigerant direct cooling system; this welder combines deep penetration capabilities with superior energy efficiency. Its integrated structural design and lightweight, ergonomic torch (just 595 grams) make it an ideal tool for high-precision and extended welding sessions, effectively protecting against operator fatigue.
The Strata SLR5000 can weld an impressive range of materials, including aluminium, stainless steel, carbon steel, galvanised sheets, and brass, with the versatility to handle thicknesses from 0.2 mm up to 9.0 mm. This welder is 6-10 times faster than traditional TIG welding on thinner materials and eliminates the need for post-weld processing, saving significant time and cost. Its focused laser beam creates low heat spread, preserving the material's appearance and structure and reducing the risk of warping or discolouration.
With eight built-in safety checks, an app for parameter adjustments and troubleshooting, and continuous operational capability for 24/7 production, the Strata SLR5000 is a robust choice for demanding applications. It has proven highly effective in sectors such as stainless steel tank and aluminium fabrication, sheet metal production, and medical equipment manufacturing. Additionally, its low shielding gas requirements and improved fume control make it both a cost-efficient and environmentally friendly option, ideal for workshops focused on efficiency and safety.
Applications in Industry
One of the advancements in modern laser welding systems is real-time monitoring. By tracking parameters such as laser power, beam focus, and welding speed, operators can adjust settings dynamically to accommodate inconsistencies in materials or joint fit-up. This adaptability helps ensure quality and repeatability, even when welding materials with slight variations.
Adaptive control enables welders to handle a broader range of materials and applications, supporting diverse industries like aerospace, automotive, and electronics manufacturing. These systems are valuable for workshops aiming to improve productivity without compromising quality.
In addition to real-time monitoring, the Strata SLR5000 also features app integration, allowing operators to control welding parameters directly from their mobile devices. This intuitive app lets users easily adjust settings for different material thicknesses, monitor machine performance, and access troubleshooting tips without interrupting their workflow. The app's remote control functionality provides a streamlined way to ensure weld consistency and quality across varying applications, from sheet metal production to medical equipment fabrication. For those new to the system, Strata offers video instructions that demonstrate setup and operation for optimal results.
Laser welding is employed across multiple industries, from the automotive sector, where speed and precision are critical, to electronics manufacturing, where minimal heat-affected zones are necessary for delicate components. Aerospace companies benefit from laser welding's ability to create solid and lightweight joints, critical for aircraft performance and safety.
Practical Tips for Implementing Laser Welders in Workshops
For workshops, the following tips can help maximise the benefits of laser welding:
- Test Parameters on Sample Materials: Before beginning production, test power, speed, and focus settings on sample pieces. This step saves time and material by reducing defects in the final products.
- Use a Thickness and Speed Chart: Reference charts provide a quick overview of optimal settings for various metals and thicknesses, simplifying adjustments.
- Invest in Monitoring Equipment: Real-time feedback allows technicians to make on-the-spot adjustments, preventing issues and maintaining consistent quality.
- Train Staff on Equipment: Laser welding technology is evolving. Regular training keeps operators updated on best practices and troubleshooting techniques.
Maintain Clean Workspaces: Reflective materials, such as aluminium, benefit from clean surfaces that reduce reflection and improve absorption.
Laser welding is a powerful tool in modern fabrication, offering precision, efficiency, and versatility. By understanding the interplay between laser power, welding speed, and material thickness, industrial technicians can achieve high-quality welds with minimal waste and downtime.
Investing in quality laser welding equipment and monitoring systems is essential for workshops looking to streamline their welding processes and stay competitive. Proline Industrial provides a range of advanced welding solutions designed to meet the demands of modern fabrication. Explore Proline’s laser welding equipment today to enhance your workshop's productivity and quality.