Table of Contents
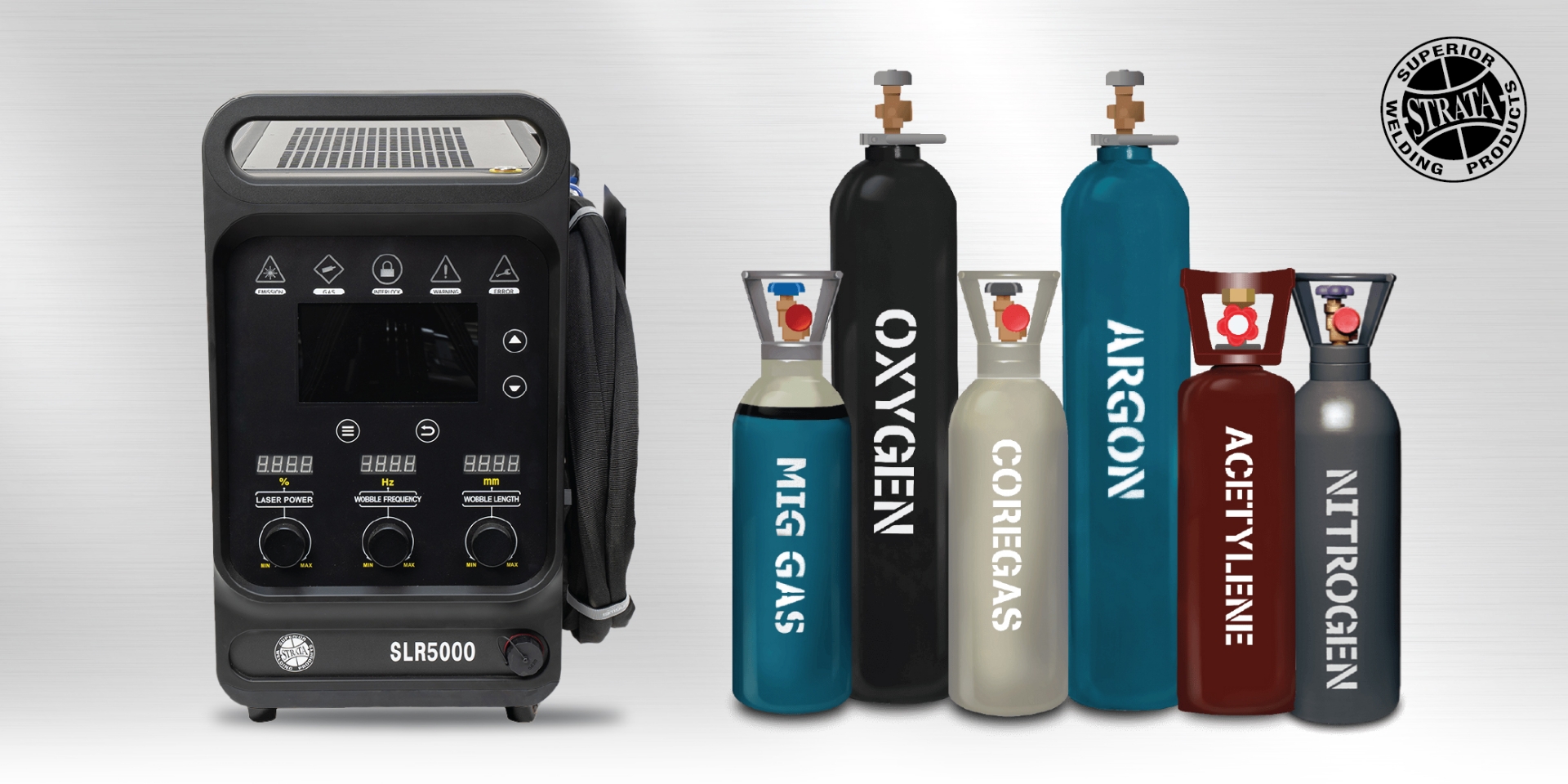
In the world of laser welding, precision and quality are paramount. Shielding gas plays a crucial role among the many factors that contribute to achieving the perfect weld. Shielding gases help prevent oxidation, control spatter, and maintain a stable weld pool, essential for producing high-quality, consistent results in laser welding applications. Selecting the correct shielding gas, the appropriate flow rate and the blowing method can significantly affect weld integrity and operational efficiency.
In this guide, we'll explore the purpose of shielding gas in laser welding, examine the most commonly used gases, and provide practical insights to help welding technicians and engineers make the best choices for their specific applications.
The Purpose of Shielding Gas in Laser Welding
Laser welding uses a high-energy laser beam to melt and join metal surfaces. However, the laser's high temperature can cause metal vaporisation, forming a metal vapour plasma that may absorb or refract the laser beam, reducing the energy reaching the weld surface. This can result in instability in the molten weld pool and, ultimately, a weaker weld. Shielding gases counteract this effect by suppressing plasma formation and protecting the weld pool from oxidation.
Beyond stabilising the weld pool, shielding gas improves overall weld quality by reducing spatter, making the weld surface more uniform, and enhancing the penetration and shape of the weld seam. It also helps control the heat-affected zone (HAZ), which minimises thermal distortion in the surrounding areas, preserving the material's structural integrity.
Benefits and Drawbacks of Shielding Gas
When used correctly, shielding gases provide a range of benefits, including:
- Reduced Oxidation: The gas isolates the weld pool from air exposure, preventing oxidation and preserving the weld's aesthetic and structural quality.
- Lower Spatter: Shielding gases can minimise spatter, reducing post-weld cleaning and improving finish quality.
- Enhanced Weld Shape: The suitable gas can create a smoother, more uniform seam by evenly distributing the weld pool during solidification.
- Improved Laser Efficiency: Reduced plasma interference allows the laser's energy to be used more effectively, increasing welding precision.
- Reduced Porosity: Shielding gas minimises porosity in the weld, which is essential for maintaining weld strength and durability.
However, incorrect use of shielding gas can have undesirable effects:
- Poor Weld Quality: Using the wrong gas type or flow rate may lead to cracks or an uneven weld, compromising strength and durability.
- Increased Oxidation: If the flow rate is too high or too low, it may increase oxidation or disturb the weld pool, creating an inconsistent weld.
- Ineffective Protection: An inappropriate gas type or improper blowing method may result in insufficient protection, reducing weld integrity.
The correct gas type and application method are essential for achieving optimal weld quality.
Types of Shielding Gases
Three primary gases are commonly used in laser welding: Nitrogen (N₂), Argon (Ar), and Helium (He). Each has unique properties that affect the weld seam differently, depending on the type of metal being welded and the specific application requirements.
Nitrogen has moderate ionisation energy, which helps to reduce plasma formation and improve laser effectiveness. While Nitrogen is not ideal for aluminium or carbon steel due to its tendency to form nitrides, it works well with stainless steel, enhancing weld strength. However, its use should be carefully considered for metals sensitive to Nitrogen's chemical effects, as it can reduce weld toughness.
Argon, a commonly used shielding gas, has low ionisation energy, making it susceptible to forming plasma clouds. However, it is a cost-effective and highly inert option, reducing the chance of reacting with metals. Due to its high density, Argon sinks effectively over the weld pool, providing a stable protective layer. It is suitable for various metals and works well in general welding applications.
Helium has the highest ionisation energy of the three, allowing superior plasma control and effective laser use. Due to its low activity, it does not react with metals, making it ideal for heat-sensitive applications and high-value welds. However, helium's high cost often limits its use in research or specialised products where weld quality is paramount.
For customers needing reliable shielding gases, Proline Industrial offers a range of gas cylinder options, including ownership, rental, and Trade N Go cylinders, which support various laser welding applications. These cylinders provide access to high-quality gas options, including Nitrogen, Argon, and Helium, essential for achieving optimal weld quality across different metals. Proline Industrial's gas cylinders are available in various sizes, accommodating small-scale projects and high-volume industrial applications. By offering flexibility in gas types and volumes, Proline Industrial makes it easy for businesses to maintain consistent weld quality and meet the specific needs of each job. For more information on available gases and cylinder sizes, reach out to their knowledgeable team.
Blowing Techniques and Angle Settings
Applying shielding gas is as important as the choice of gas itself. The two main blowing techniques in laser welding are side-axis side-blowing and coaxial blowing.
- Side-axis Side-blowing: This technique directs the shielding gas from the side, creating a broad area of coverage and protecting both the molten pool and the newly solidified weld. This is ideal for applications like linear welds on flat materials.
- Coaxial Blowing: In coaxial blowing, the gas flows directly from the laser head, providing concentrated protection over the weld pool. This method is preferred for intricate welds or when working with closed graphical patterns.
In addition to the method of blowing, the angle of the gas flow significantly affects the weld outcome. Studies have shown that a 30° angle provides optimal penetration and stability in the weld pool, while a 45° angle maximises surface width. Choosing the right angle based on desired properties helps control penetration, surface quality, and weld shape.
Practical Tips for Industrial Workshops
Here are some practical tips for using shielding gases effectively in laser welding:
- Test Parameters on Sample Materials: Before full production, test different gases, flow rates, and angles on samples to determine the best combination for each material type.
- Adjust Flow Rate According to Thickness: Thinner materials typically require a lower flow rate, while thicker materials benefit from increased gas flow for better protection.
- Experiment with Blowing Angles: For deeper penetration, try a 30° angle, and for broader surface coverage, consider 45°. Adjust based on weld requirements and metal properties.
- Use High-Quality Equipment: A reliable gas flow system and monitoring tools ensure consistent gas coverage and weld quality.
The right shielding gas choice is critical to achieving consistency in laser welding applications. Industrial professionals can significantly improve their welding results by understanding the properties of Nitrogen, Argon, and helium and using effective blowing techniques and angle settings.
Strata Pro Series Laser Welders for Every Welding Job
For welders seeking high-performance equipment compatible with various shielding gases, the Strata SLR3000 and SLR5000 laser welders are exceptional choices. Equipped with "small core diameter" laser technology, these models deliver deep weld penetration across various metals, from stainless steel to aluminium and brass. The SLR3000 is suited for medium-duty applications, providing efficient, controlled welding for smaller-scale projects. The SLR5000, the other hand, offers more power for intensive or high-volume jobs, making it ideal for heavy-duty applications.
Both laser welders work seamlessly with shielding gases like Nitrogen, Argon, and Helium, optimising weld quality with minimal heat spread and enhancing productivity. The SLR Pro Series laser welders are designed to meet the demands of modern workshops, offering efficiency, consistent weld results, and durable construction for reliable, long-term use.
Achieving consistent, high-quality results in laser welding depends on optimising equipment and shielding gas selection. The Strata SLR3000 and SLR5000 laser welders are designed to deliver precision, working seamlessly with shielding gases like Nitrogen, Argon, and Helium to enhance weld penetration and minimise oxidation. By pairing these advanced welders with the right gas and application techniques, welders can create smoother, durable welds with reduced spatter and less need for post-processing. Whether working with stainless steel, aluminium, or other metals, Proline Industrial's range of shielding gases and high-performance laser welders provide a comprehensive solution for any welding job. For those looking to elevate their welding setup, Proline Industrial offers the tools and expertise to achieve professional results.