Table of Contents
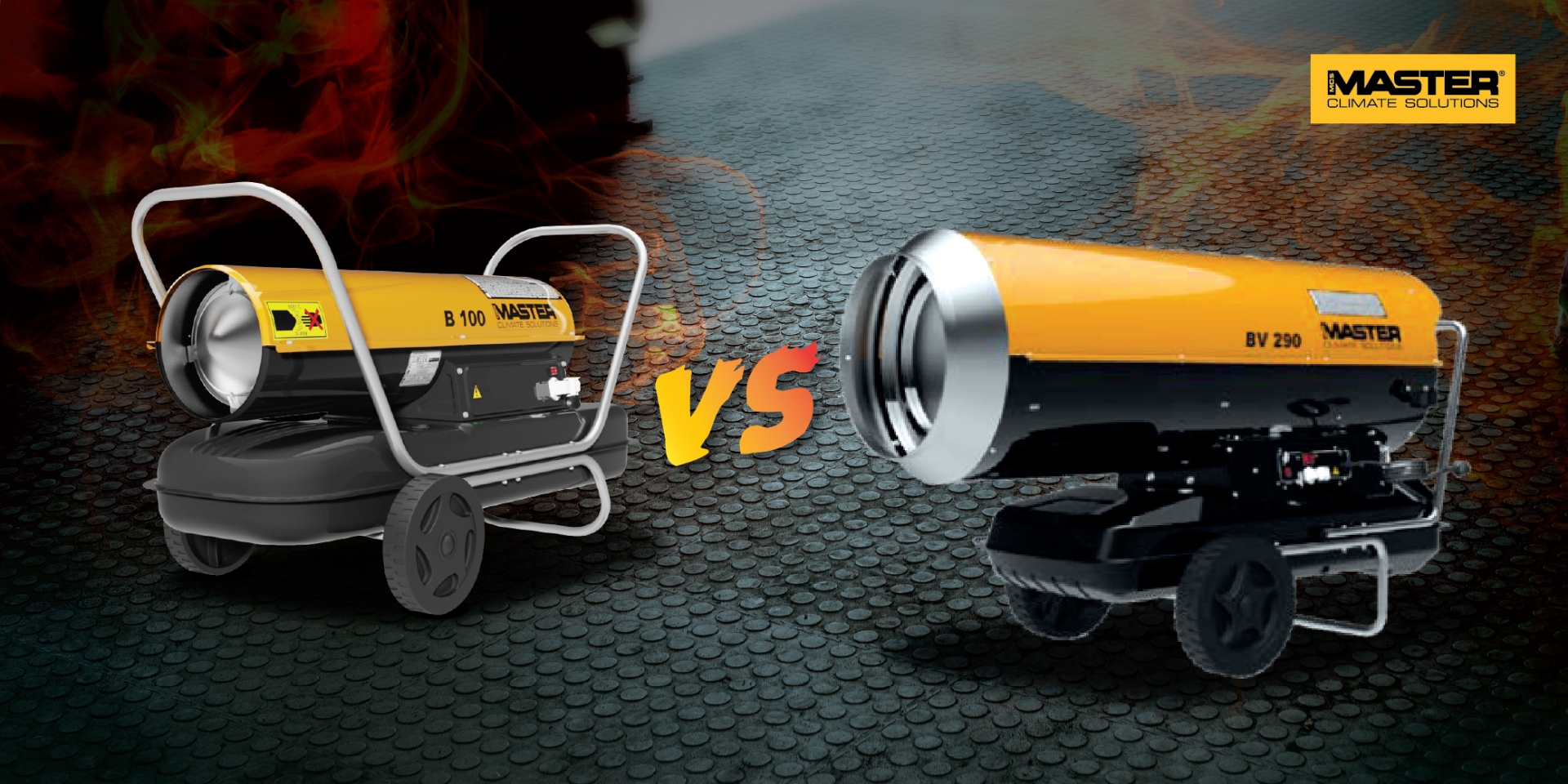
Maintaining a warm, safe working temperature is essential during the colder months in New Zealand industrial environments such as workshops, factories, warehouses, and construction sites. Diesel-fired heaters are popular thanks to their high heat output and portability. When selecting a diesel heater, one of the most important considerations is whether to use a direct-fired or an indirect-fired model. Each has specific advantages and limitations depending on the nature of the workspace and ventilation available.
Understanding the differences between these two types of heaters ensures that businesses can make informed decisions to maximise efficiency, safety, and cost-effectiveness. This article explores how each type operates, their pros and cons, and their ideal applications, with product examples from the Master 29 kW Direct Forced Air Diesel Heater and the Master 85 kW Indirect Forced Air Diesel Heater.
What Is a Direct-Fired Diesel Heater?
A direct-fired heater burns diesel fuel to generate a flame inside an open combustion chamber. A fan blows air directly across this flame, warming it before distributing it into the space. The air that passes through the combustion area carries some by-products, such as water vapour and carbon dioxide, into the environment.
Direct-fired heaters are highly efficient—nearly all the energy from the fuel is transferred into heat. Their portability and low maintenance make them ideal for well-ventilated spaces or outdoor work areas.
Direct-Fired Heating in Action: The Master 29kW Heater
A standout option in the direct-fired category is the Master 29kW Air Forced Diesel Heater, a robust and fuel-efficient heater well-suited for New Zealand workshops, warehouses, factories, and construction sites. Italian-made and built for industrial conditions, this unit delivers fast, reliable warmth for areas up to 265 m², making it an ideal solution during the colder months. Its 44-litre diesel tank allows up to 16 hours of continuous operation, reducing the need for frequent refuelling. Key features such as electronic flame control, dual fuel filters, a stainless-steel combustion chamber, and a thermally protected motor provide enhanced safety and operational longevity. This heater is designed with performance in mind and offers a practical solution where quick, portable heat is essential.
Advantages of Direct-Fired Heaters
- High Fuel Efficiency: Almost 100% of the diesel burned is converted into heat, resulting in excellent fuel economy.
- Lower Purchase and Running Costs: These heaters typically have fewer components, which keeps initial costs and ongoing maintenance to a minimum.
- Portable and Simple: Direct-fired heaters are easy to relocate and operate due to their lightweight design and simple functionality.
- Quick Warm-Up: The heated air flows directly over the flame, so the temperature in the target area rises very quickly.
Limitations of Direct-Fired Heaters
Despite their benefits, direct-fired heaters come with specific limitations:
- Air Quality Concerns: The heated air contains combustion by-products, including carbon monoxide, CO₂, and moisture traces. These are unsuitable for enclosed spaces, especially where people are present.
- Ventilation Requirement: Direct-fired heaters should only be used in environments with adequate airflow. Otherwise, they pose a risk to health and safety.
- Not for Flammable Environments: Direct-fired heaters are unsafe in areas with flammable materials or vapours because of the open flame.
What Is an Indirect-Fired Diesel Heater?
An indirect-fired diesel heater isolates the flame from heated air using a sealed combustion chamber. Instead of blowing air directly across the flame, it passes over a heat exchanger that the combustion process has warmed. This results in clean, fume-free warm air being distributed into the environment while the exhaust gases are vented through a flue—essentially acting like a mobile furnace with a chimney.
This separation of combustion and heated air makes indirect-fired heaters ideal for enclosed or poorly ventilated spaces, including areas occupied by workers or sensitive materials.
Clean, Reliable Heat for Large Spaces: The Master 85kW Heater
For industrial spaces that demand safe, fume-free heat, the Master 85kW Indirect-Fired Heater is a dependable solution designed to perform in challenging New Zealand environments. Ideal for heating large enclosed areas such as factories, warehouses, and construction sites, this unit delivers high-capacity output capable of warming up to 785 m² efficiently. Its 105-litre fuel tank supports up to 13 hours of operation, offering extended runtime without constant refuelling. Built with a stainless-steel combustion chamber, electronic flame control, and a thermally protected motor, this heater ensures safe, consistent heat. Practical features like an oil level indicator, compact dimensions for its capacity, and a design focused on easy maintenance and mobility make it a strong choice for professionals who require clean air heating without compromising reliability.
Advantages of Indirect-Fired Heaters
- Clean Heated Air: The separation of the combustion process ensures that only warm, clean air is delivered. This is essential for any workspace where air quality is a priority.
- Safe for Enclosed Spaces: Indirect-fired heaters are safe for environments with people, animals, or sensitive products.
- Reduced Moisture: Since the combustion by-products are vented out, indirect heaters do not add unwanted humidity to the space.
- Versatility with Ducting: These heaters can be placed outside the workspace and have warm air ducted in, making them flexible regarding placement and operation.
Limitations of Indirect-Fired Heaters
- Higher Costs: The additional components, such as the heat exchanger and flue system, make indirect heaters more expensive to buy and maintain.
- Lower Efficiency: Some heat is lost during the transfer process, meaning slightly higher fuel consumption than direct-fired models.
- Larger and Heavier: Indirect heaters tend to be bulkier and may require more effort to transport and set up.
Choosing the Right Heater
Selecting the best heater for your application depends on several key factors:
Space Type: A direct-fired heater will be more efficient and cost-effective if the space is open and well-ventilated. An indirect heater is safer if it’s enclosed or poorly ventilated.
Occupancy: Indirect-fired heaters are recommended for occupied areas or those containing sensitive goods or animals due to their clean air output.
Budget: Direct-fired heaters are less expensive and have lower operating costs. Indirect heaters, while costlier, provide the necessary safety and air quality in enclosed applications.
Heating Purpose: Use direct-fired heaters for quick, short-term heating in ventilated zones. Indirect heaters are better suited for long-term, safe heating of enclosed or sensitive environments.
Application Examples
- Construction Sites: Use direct-fired heaters during the early phases of construction where ventilation is not an issue. Use indirect-fired models during the finishing stages or when working indoors.
- Workshops: Direct-fired heaters offer efficiency in large, well-ventilated workshops. In smaller or enclosed shops, indirect-fired heaters ensure safe and clean heating.
- Events and Marquees: Indirect-fired heaters provide odourless, safe heating for public spaces.
- Warehouses and Storage: Indirect-fired heaters help maintain temperature without affecting product quality.
Choosing between a direct-fired and an indirect-fired diesel heater ultimately depends on the specific demands of the workspace, the level of ventilation available, and the importance of maintaining air quality. Direct-fired heaters, such as the Master 29kW, are well-suited to ventilated environments requiring rapid, efficient heat. Their lower purchase and operating costs make them a practical choice for open workshops, construction sites, and similar applications.
On the other hand, indirect-fired heaters like the Master 85kW provide clean, fume-free heat, making them ideal for enclosed or occupied spaces such as warehouses, event marquees, or indoor construction areas. Though typically more expensive to purchase and maintain, their safety, versatility, and ability to maintain air quality in sensitive environments justify the investment.
Each heating solution serves a distinct purpose. A direct-fired heater offers simplicity and speed where conditions allow, while an indirect-fired model ensures comfort and safety in controlled environments. Matching the heater to the job ensures optimal performance, protects personnel and equipment, and supports uninterrupted productivity through the colder months.
Proline Industrial offers a trusted range of Master diesel heaters to suit all industrial and commercial needs. Talk to the team today to find the right heater for the job.